摘 要:盾构竖井深基坑围护结构体系的稳定对保证盾构施工的安全至关重要。以北京地铁10号线某盾构井深基坑工程为例,通过数值模拟,分析支撑轴力和桩体水平位移的相互作用机理,并与现场监测结果进行对比。研究结果表明:基坑钢支撑的轴力均在安装完后不久达到最大值,然后减小并逐渐趋于稳定,最大位置发生在角撑;钢支撑对桩体水平位移的发展有一定的限制作用,桩体最大水平位移的位置随基坑开挖逐渐下移。
关键词:深基坑;围护结构;现场监测;数值模拟
0引言
地下工程的快速发展,使城市深基坑工程的建设环境越来越苛刻,造成设计与施工的困难。另外,由于地质条件、施工方式、荷载水平等因素的复杂性,使理论分析变得困难。因此,深基坑支护结构体系的现场监测与数值仿真计算对安全施工意义重大。利用弹性地基梁法和有限差分法,分别计算深基坑开挖过程中桩锚支护结构的变形和内力,并与实测数据对比分析;研究结果表明理论值与实测值存在差别,建立理论模型比较困难。通过现场测试,对土体力学特性在不同开挖阶段的变化进行了研究。研究结果表明:预应力锚索支护结构能有效地控制深基坑变形及地表沉降,从而能够确保深基坑自身的安全。目前,大多数分析是基于某一单独指标的实验室试验或现场测试,未全面研究支护结构体系各个指标之间的相互影响机理。
本文以北京地铁某一盾构井深基坑工程为背景,采用FLAC3D对其进行数值模拟,分析支撑内力与桩体水平位移的相互影响机理,并与现场监测结果进行对比。研究结果可指导工程施工,确保盾构井深基坑工程的安全和稳定。
1工程概况
北京地铁10号线2期巴沟段盾构竖井基坑长21.00m,宽18.00m,基坑呈长方形,开挖深度18.66m。盾构井围护结构采用钻孔灌注桩加钢支撑结构,桩长21.50m,共设3道钢支撑。第1道钢支撑设于冠梁处,第2、3道钢支撑通过水平钢围檩支撑在钻孔灌注桩上;第1、2道钢支撑间距为9.05m;第2、3道钢支撑间距为5.30m。地层自上而下大体分为:人工填土层、粉土层、粉细砂层、卵石圆砾层、细中砂层和卵石层。各土层的岩土工程特征描述见表1。地质勘察发现卵石圆砾层底部含潜水,水量较小,其他地层未发现地下水。
2计算模型及结果分析
2.1几何模型的建立
数值仿真计算采用FLAC3D有限差分计算软件。根据盾构井的几何尺寸以及深基坑开挖的影响范围,本工程模型的长、宽、深几何尺寸分别为105.00m×90.00m×58.75m。模型尺寸考虑了边界条件对计算结果的影响。几何单元网格见图1。
表1 土层的基本力学参数
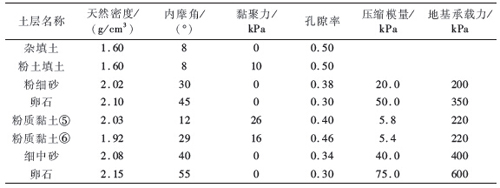

图1 几何单元网格
2.2边界条件
在进行模拟的过程中,模型边界约束条件设定如下:模型侧面和底面为位移边界,模型侧面的位移边界条件是约束水平移动;模型底部位移边界为固定边界,约束其水平移动和垂直移动。模型上边界为地表,为自由边界。
2.3模型选择与结构单元
结合北京地区土质特性,模型中岩土体的破坏准则采用Morh Coulomb屈服准则描述。采用软件自带的“pile”单元来模拟混凝土钻孔灌注桩。混凝土钻孔灌注桩桩径采用0.80m,桩距1.40m,弹性模量取30Gpa,泊松比取0.2。考虑到以受压为主,采用“beam”单元来模拟钢支撑,其直径为0.63m、厚度为12mm,弹性模量取250GPa,泊松比取0.3。采用“shell”单元模拟喷射混凝土的作用,弹性模量取14.2GPa,泊松比取0.20,厚度取0.10m。为了考虑桩体结构与土体之间的共同作用,在两者之间设置“interface”接触面单元。
2.4计算结果分析
基于工程实际情况,计算得到了基坑不同开挖深度的桩体水平位移图以及钢支撑轴力图。
2.4.1桩体水平位移
基坑开挖到-9.50m并安装第2道钢支撑后,桩后土体最大水平位移的位置向下移动,发生在第1道支撑与第2道支撑之间。桩后土体水平位移最大值约为5.60mm,这与悬臂桩相异,悬臂桩结构的最大位移出现在顶端,但是由于钢支撑的侧限作用,使得最大水平位移的位置下移,如图2a所示。基坑开挖至设计深度后,桩后土体水平位移的最大值达到9.50mm,位于第2道与第3道钢支撑之间,如图2b所示。
图2 基坑开挖过程中的桩后土体水平位移(单位:m)
2.4.2钢支撑轴力
图3a~图3d分别为架设4道钢支撑时轴力的计算结果。计算结果表明:架设第1道钢支撑后,该层钢支撑的轴力最大值发生在角撑,最大值为131.4kN/m。在完成第2层钢支撑的架设后,随着基坑开挖,第2层支撑内力即达到最大值205.8kN/m,最大值仍发生在角撑,第1层钢支撑内力在第2层钢支撑架设后迅速减小,并远小于设计值的205kN/m。随着基坑的开挖及第3层钢支撑的安装,3层钢支撑共同分担土体压力,第1层钢支撑轴力继续减小,而第2层钢支撑轴力增加的趋势也逐渐放缓,随着基坑开挖到设计深度附近,第3层钢支撑轴力也达到最大值135.3kN/m。在模拟完成基坑土体开挖及浇注完成底板之后,第1层、第2层及第3层钢支撑的轴力均有所减小。基坑开挖过程中,角撑的计算轴力明显大于直撑的计算轴力,支撑的轴力均在安装完后不久达到最大值,然后减小并逐渐趋于稳定。
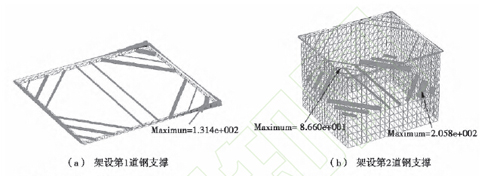
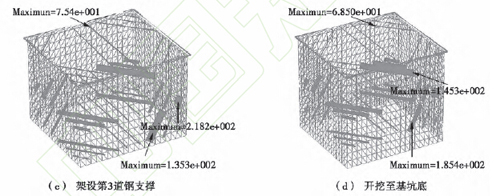
图3 基坑开挖过程中的钢支撑内力图(图中所示为每层钢支撑最大轴力,单位:kN)
2.4.3对比分析
计算结果表明:随着每层支撑的架设,变形速度明显减少,且位移最大值位置始终位于远离支撑处。
3现场监测
3.1监测方案
监测方案的制定是为了反映施工期间整个基坑的变形情况,以达到各种测试结果、作用关系相互验证的目的。具体监测测点布置图见图4。
3.2桩体水平位移监测结果
图5为各关键施工阶段桩身水平位移曲线。由图5可知:基坑开挖过程中最大水平位移发生位置逐渐下移,在顶板完成后,桩体最大水平位移为10.10mm,位于距离地表-8m的位置处。架设第1道钢支撑时,由于开挖深度不大,故水平位移相对较小。第2道钢支撑架设完成后,最大水平位移位置逐渐下移于第1道钢支撑与第2道钢支撑之间,这与数值计算结果基本一致。架设第3道钢支撑后,水平位移继续下移,但是没有下移到第2道钢支撑与第3道钢支撑之间,与数值计算结果有所差异。其主要原因为:施工中的钢支撑架设略慢于计划时间,导致桩体水平位移有所发展后,才完成钢支撑的架设,这时因开挖造成的桩体水平位移已基本完成,故架设钢支撑后,桩体水平位移变化不大,导致最大水平位移位置下移不明显。此种差异也表明了在钢支撑达到设计荷载时,可以对桩体水平位移起到明显的限制作用,及时架设钢支撑对基坑的整体稳定至关重要。
图4 基坑监测点布置图
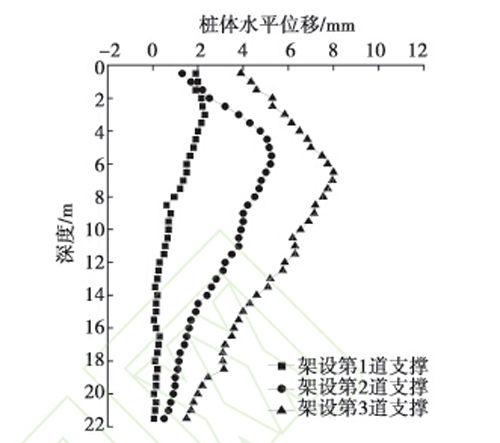
图5 各关键施工阶段CX1桩身水平位移曲线
3.3监测结果分析讨论
通过数值模拟与现场实测数据的对比表明两者结果基本吻合,这说明桩体水平位移实际变化与理论研究规律是符合的。综合分析上述计算结果和现场监测数值,在基坑开挖过程中,钢支撑与桩体水平位移的相互作用大致可表述为几个方面:(1)架设第1道钢支撑前,基坑处于暴露状态,围护桩呈现向基坑坑内变形前倾型曲线,桩顶水平位移最大;钢支撑施加后,围护桩桩体水平位移变形曲线由前倾型向弓形变化。(2)架设第2道钢支撑后,桩后土压力从桩体自身承担逐渐转移为由桩体和钢支撑共同承担。此时第1道钢支撑轴力有所减小,同时,由于加入了第2道钢支撑的侧限作用,使得桩体最大水平位移的位置下移至第1道与第2道支撑之间,如图3b所示。(3)第3道钢支撑的架设使得钢支撑承担的土压力比重增大。在整个开挖过程中,第2道钢支撑轴力始终最大,故第2道钢支撑应作为监测的重点。支撑与桩体水平位移的相互作用表明:钢支撑的架设时机以及所施加轴力的大小对桩体水平位移的影响较大,对基坑的整体稳定至关重要。
4结论
(1)基坑钢支撑的轴力均在安装完后不久达到最大值,后随之减小并逐渐趋于稳定,最大位置发生在角撑。在整个基坑开挖过程中,第2道钢支撑轴力始终最大。
(2)钢支撑对桩体水平位移的发展有一定的限制作用,桩体最大水平位移的位置随基坑开挖逐渐下移。钢支撑的架设时机以及所施加轴力的大小对桩体水平位移的影响较大。
(3)数值模拟结果与现场实测数据基本吻合,说明桩体位移变化与理论研究规律是相符的,对盾构井深基坑围护结构的设计施工有一定的借鉴意义。
作者:李涛,王昕鹏,陈慧娴,杨成淳,黄佩格
转自:《河南科技大学学报》
评论 (0)